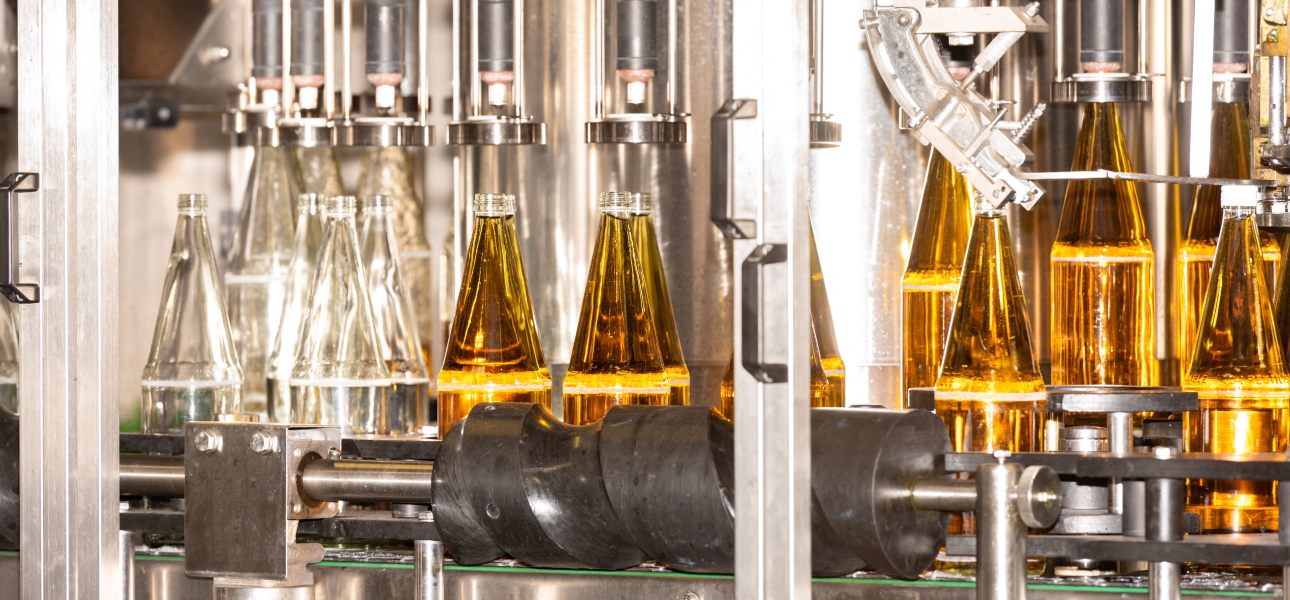
Dosing technology
The dosing systems used in the field of dosing technology are being continuously optimized and advanced. The function of dosing systems is to guarantee on-demand or continuous delivery, dosing, application, non-traditional machining and removal of materials depending on the field of application. This is where plants and systems are used across a range of areas such as material processing, during process controls and joining processes of the type used in bonding technology or micro-dosing.
Learn more
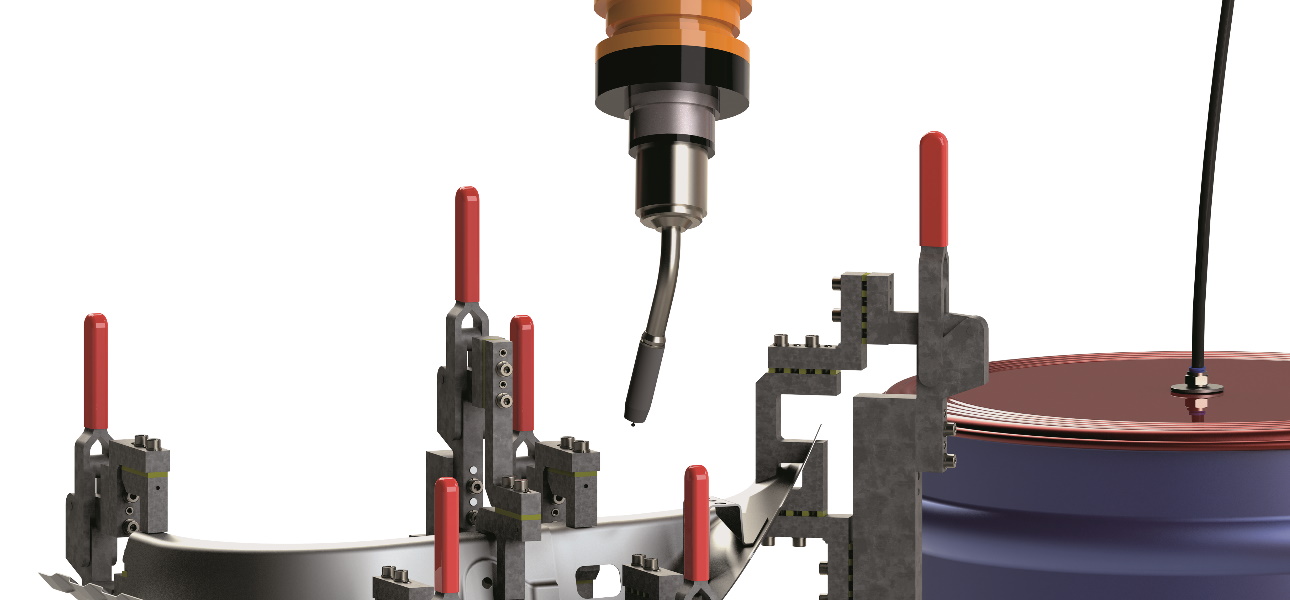
Joining technology
Joining is one stage of the assembly process and describes the operation by which two or more components of defined geometric shape, the adherends, are permanently joined to one another. Under certain circumstances, this is carried out using an additional substance, such as adhesive, as an auxiliary agent. Joining produces an interlocking connection at the respective joints of the components. The resulting workpiece connections can be further classified into separable connections such as bolted connections, inseparable connections such as welded connections and connections using rivets or solder that offer limited scope for separation.
Learn more
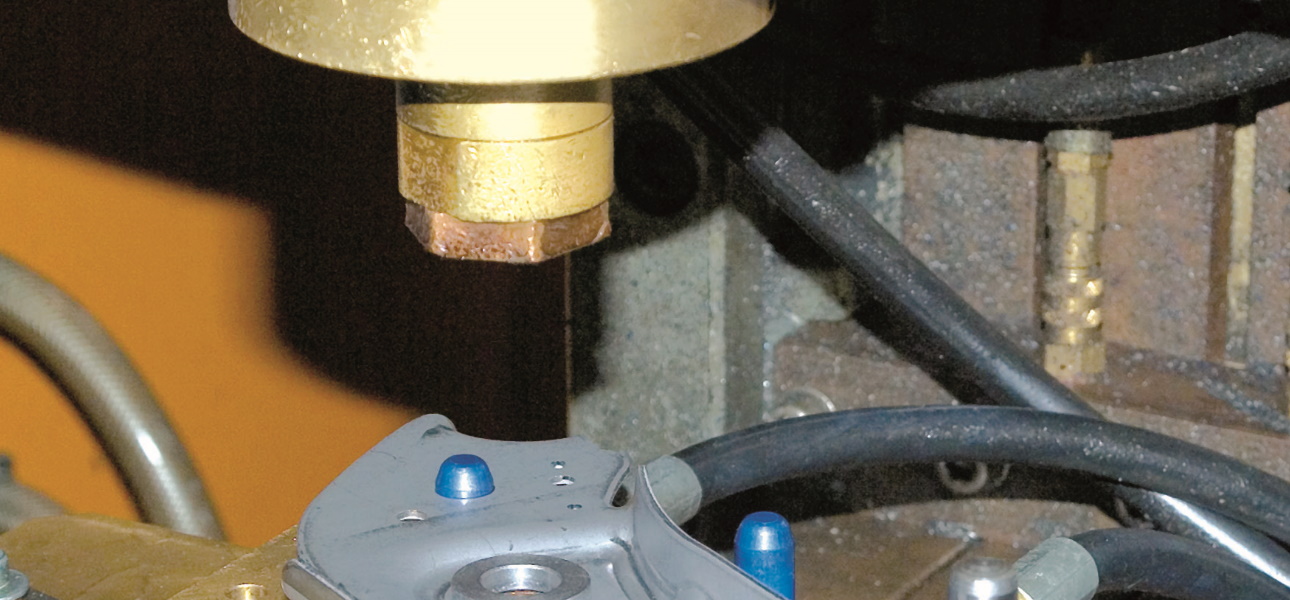
Handling technology (positioning)
Despite the seemingly simple appearance of the components sometimes used, a great deal of attention goes into the concepts employed in the area of handling technology. The component must work repeatedly with very high positioning accuracy and without damaging the part being handled. The material used must be virtually wear-free and resistant to all media and environmental parameters. Furthermore, no traces of abrasion can be left on the component to be handled. High-performance ceramics are tailor-made for this application thanks to their inherent properties.
Learn more
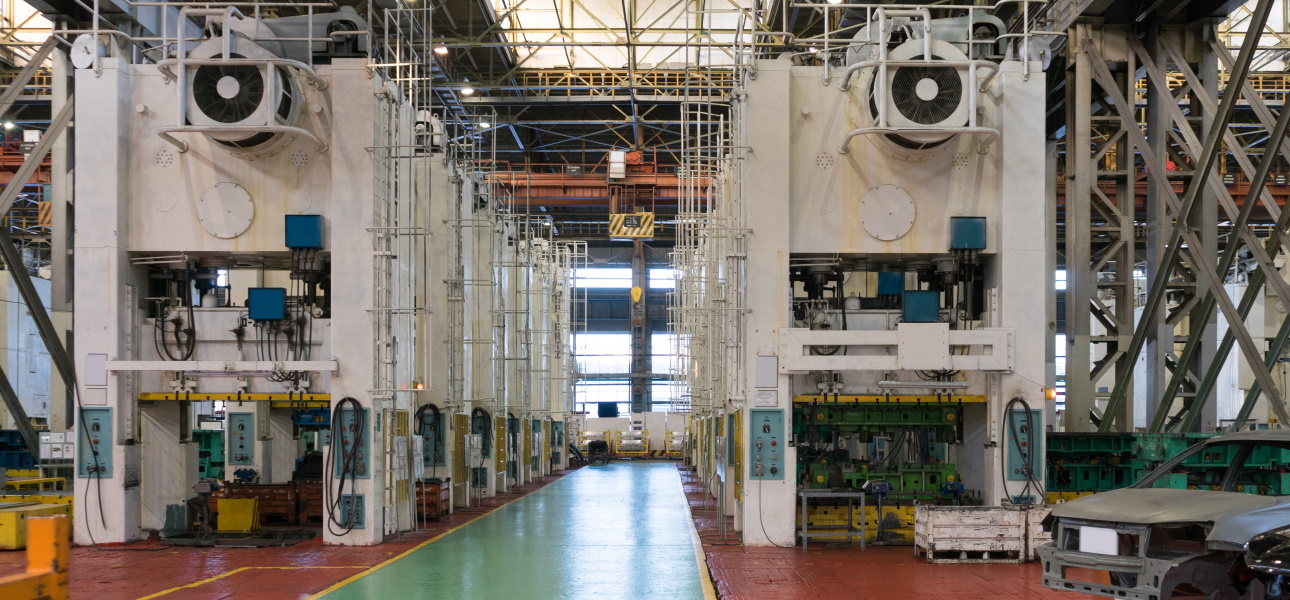
Forming technology
Metal forming, particularly in the field of metal processing, is a production process where tools are exposed to particular stresses. These arise on the one hand from particularly hard materials, such as hot-stamped sheet metals, which lead to premature tool wear as part of mechanical processing. On the other hand, these stresses arise from deposits and adhesions, for example, from aluminium on steel tools.
Learn more
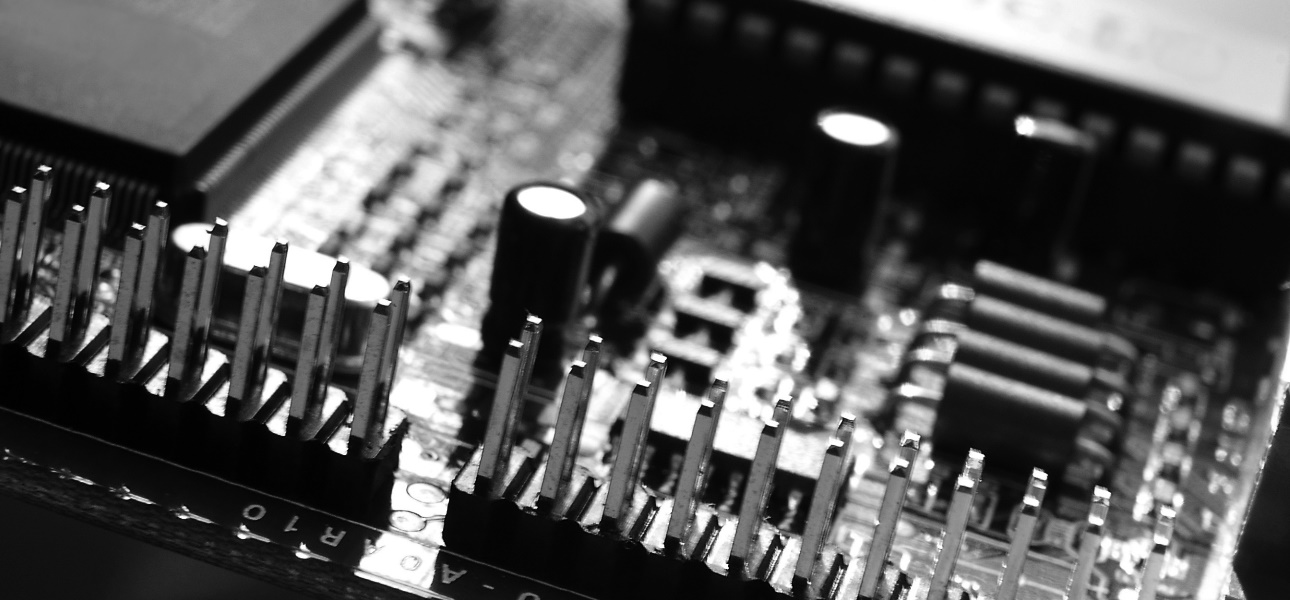
Test technology
The final stage of every manufacturing process is the testing of the component. Test technology concerns itself with the End-of-Line test (EOL test) for electronic and mechatronic component parts and assemblies. During these tests, a plug is used to check the contacts in the mating connector of the component to be tested. The software is then installed, the function tested or a stress test on the electronics is conducted.
Learn more
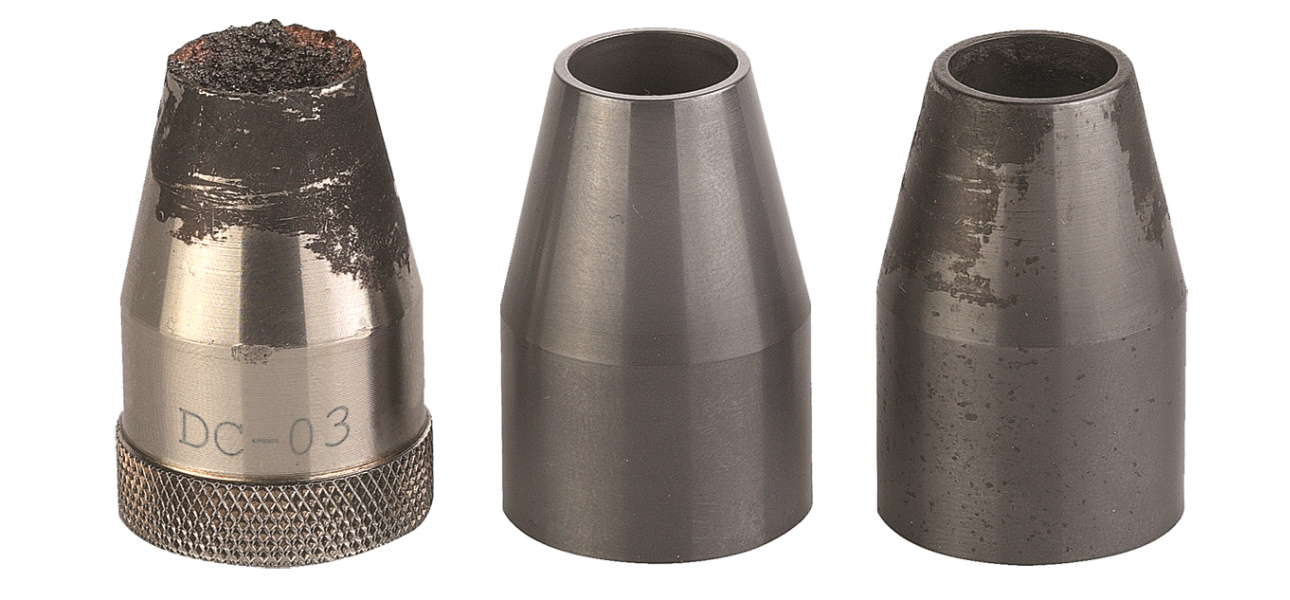
Wear-protection technology
Wear is defined as the progressive removal of material from a surface as a result of mechanical, chemical or thermal loads. It is caused by a grinding, scratching or percussive load. In most cases, the change to the surface of the material is undesirable. Reducing wear presents an important opportunity to extend the service life and useful life of machines and plants, thereby saving operating costs as well as conserving material resources.
Learn more
Our materials
The MOESCHTER Group was founded as a technology company dedicated to manufacturing user-friendly products from high-performance materials. More than two decades later, it has developed a material portfolio that covers a wide range of requirements for diverse industrial application areas.
LEARN MORE
Our solutions
We demonstrably reduce machine downtimes across a range of production processes through practical component design and by providing technical advice during the process.
LEARN MORE